Plug Valve vs Ball Valve: Applications & Use Cases
Due to their simplicity and relative durability, ball valves and plug valves are both used extensively in a wide range of piping systems.
With a full-port design that enables unrestricted media flow, plug valves are frequently used to transport slurries, including mud and sewage. They also provide bubble-tight shutoff for liquid, gas and vapor media. If fortified, their already-tight shutoff capabilities can offer a leak-tight seal against corrosive media. Their simplicity and anti-corrosion qualities make them exceedingly reliable in applications where quick, tight shutoff is critical.
Ball valves also provide a bubble-tight shut-off in fluid services like air, gas, vapor, hydrocarbon, etc. Favored for high pressure and high temperature systems, ball valves are found in gas lines, crude oil plants, tank farms, oil refineries and automated process applications. Ball valves with the highest pressure ratings can be found in underground and subsea systems. They are also popular in sanitary applications like medical, pharmaceutical, biochemical, brewing and food and beverage processing.
Which Type of Valve is Right For Your Application?
The function and design of plug and ball valves — and the differences between them — are fairly straightforward, but it always helps to speak to an expert who can guide you in the right direction.
In short, if you require an on/off valve for low- to moderate-pressure applications, a plug valve will provide a quick, leak-tight seal. For low- to high-pressure applications (especially those for which keeping torque to a minimum is critical), ball valves are a reliable, easy-to-operate solution. There are exceptions in every case, but familiarizing yourself with their specific qualities and recommended use cases is a good place to start.
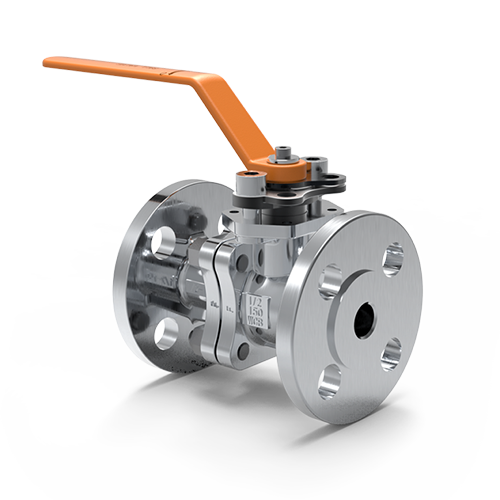
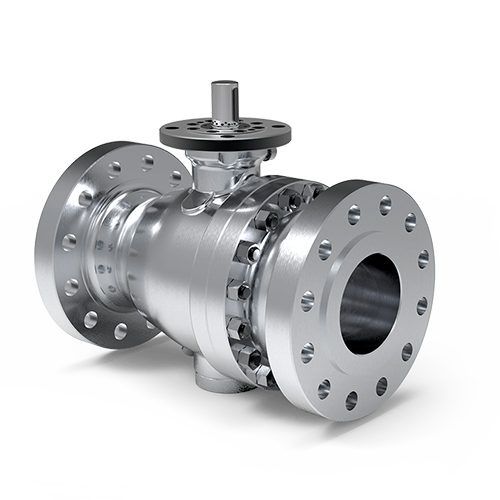
Post time: Dec-22-2022